Description
Product Specification
Module Data | MBR-10 | MBR-20 | MBR-30 |
Nominal Area (m2) | 10 | 20 | 30 |
Dimensions (mm) | 1000*535*40 | 1800*535*40
1500*630*42 |
2100*630*42 |
Recommend Flow (m3/day) | 3.0~4.5 | 5.0~7.5 | 7.5~11 |
Dry/Wet Weight (kg) | 9/18 | 18/35 | 26/50 |
Membrane Properties | |||
Membrane Material | Polyvinylidene fluoride(PVDF) | ||
Nominal Pore Size (μm) | 0.04 μm or 0.1 μm | ||
Reinforced Material | Crocheted PET | ||
Fiber Diameter | 1.2/2.6 mm | ||
Breaking Strength | >200 N | ||
Processing Method | Embedded coating | ||
Surface Properties | Non-Ionic & Hydrophilic | ||
Flow Path | Outside-In | ||
Operation & Maintenance | |||
TMP Range | -0.05 to 0.05 Mpa | ||
Operating Temperature | 5~45 oC | ||
Operating pH Range | 7.0~9.0 (consider biological) | ||
Operation flux | 10-25 L/m2·h | ||
Backwash flux | 30-60 L/m2·h | ||
Max Cleaning Temperature | 40 oC | ||
Cleaning pH Range | 1.0~13.0 | ||
Max. NaClO Concentration | 5,000 ppm | ||
Permeate Turbidity | ≦0.5 NTU |
Note: MBR-12, MBR-15, MBR-25, MBR35 and customized model are available
Why We Do
With the continuous improvement of industrialization and the deterioration of the quality of various water sources, Good chemical stability, high mechanical strength, and strong anti-pollution ability have become increasingly common requirements for the performance of membrane separation materials.
At present, hollow fiber membrane bioreactor have occupied obvious advantages in global membrane bioreactor (MBR) engineering applications.The types of hollow fiber membrane bioreactor(MBR) are mainly as homogeneous solid PVDF hollow fiber MBR and reinforced PVDF composite hollow fiber MBR. First of all, due to insufficient strength, homogeneous solid PVDF membrane has the disadvantages that the membrane fibers are frequently broken and difficult to repair during operation, which will lead to poor effluent quality and extremely short service life. Therefore, the braided tube reinforced PVDF composite hollow fiber MBR are developed for the high mechanical strength required by the MBR process, which completely solved the fiber-broken situation that has been worried by waste water industry for a long time. so the market of reinforced PVDF MBR has a bright future. The braided tube reinforced pvdf hollow fiber membrane is mainly composed of a coated surface membrane separation layer and an inner core braided tube support material, which respectively perform functions of separation and high strength.
However, the smooth surface and high weaving density of the braided tube will lead to insufficient adhesion between the two materials. And it will cause the membrane separation layer to easily peel and tear from the surface of the braided tube. As a result, the water quality is getting worse and worse, and in severe cases, it may even lead to failure and scrapping of the MBR elements.
How We Improve
Improving the bonding strength between the membrane separation layer and the inner reinforced tube is the critical technology to extend the service life of the reinforced hollow fiber membrane bioreactor. In this regard, some international companies such as Japan Mitsubishi and USA Koch have also researched and produced the reinforced PVDF hollow fiber composite membranes , all their products are with relatively high anti-peeling strength.
Hydro blue’s technology mainly uses the following two aspects to improve the reinforced PVDF hollow fiber MBR membrane.
1. Use a crocheted support tube instead of a braided support tube(Figure1). The surface of the crocheted tube is rough and full of small through holes penetrating the inner surface of the support tube. By using the controllable infiltrated and embedded composite molding processing technology, the membrane material penetrates and is firmly embedded in the inner support layer(Figure2), which greatly enhances the adhesion between the membrane separation layer and the inner support layer. Therefore, The problems of fiber-broken and fiber peeling are completely fundamental solved out in current MBR applications.
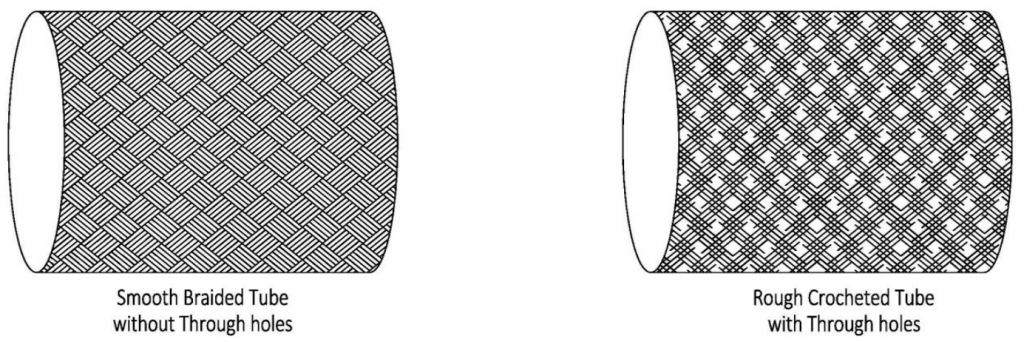
Type of Reinforced Tube
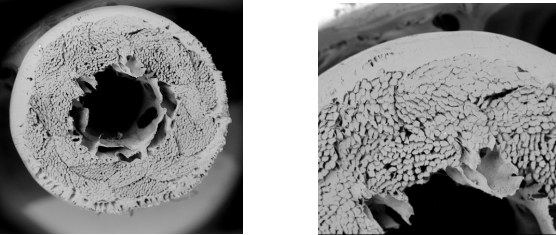
Embedded PVDF Membrane
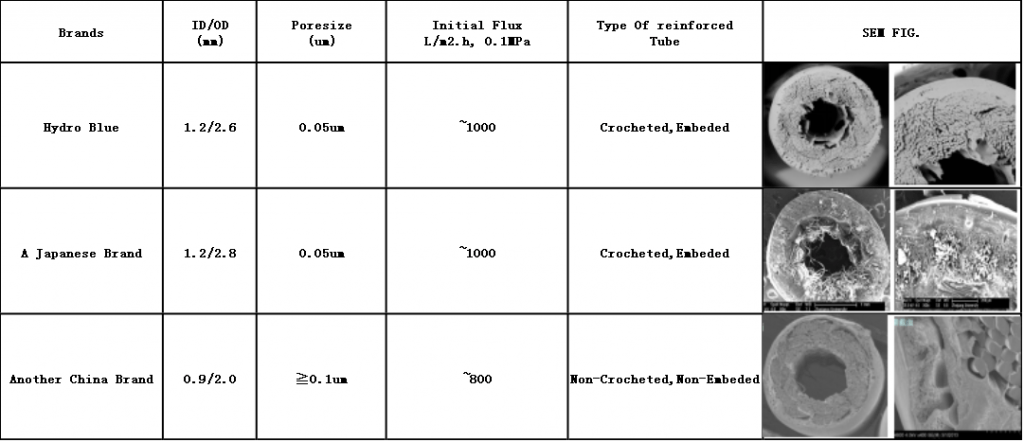
Comparison of composite MBR membrane
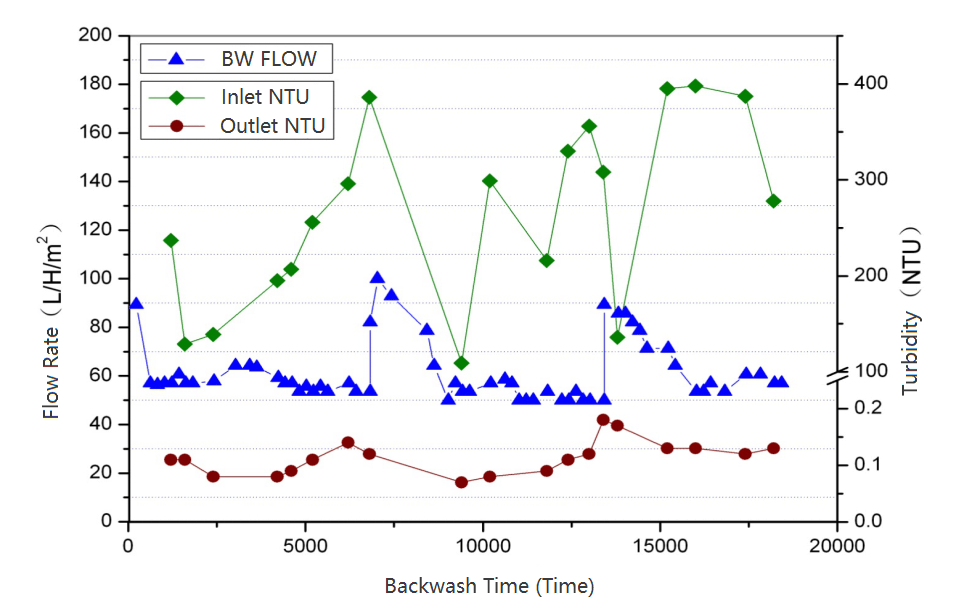
Backwash Testing for anti-peeling
Narrow Pore Size Distribution (most pores range 0.35~0.05um)
Narrow Pore Size Distribution(most pores range 0.07~0.12um)
Advantages of MBR Technology
The combination of membranes with the activated sludge process has redefined sewage & waste water treatment approach,optimizing the biological treatment operation and yielding a treated effluent that is ideal for reuse. The Key advantages in membrane technology are at the leading edge of this trend:
1.Uncoupling HRT and SRT
A significant advantage of the membrane bioreactor process is that the activated sludge are completely retained in the reaction tank. This means the sludge retention time (SRT) in the reaction tank can be completely controlled separately from the hydraulic retention time (HRT).
This is different from the CAS process, where the flocculant sludge that make up the biomass have to be allowed to grow in size to the point where they can be settled out in the secondary clarifier. In a CAS, the HRT and SRT are therefore coupled, since the floc size and thus its settlability relate to the HRT.
2.High quality effluent
Membrane’s pore size (0.04 or 0.1 µm) ensure that the permeated effluent is of very low turbidity and significantly reduced pathogen concentration. MBR processes provide a substantially clarified and disinfected effluent of high enough quality to be discharged or reclaimed for applications such as irrigation, utilities or toilet flushing.
3.Small footprint of the plant
The retention of the solids and the increase in SRT to generate higher biomass solids concentrations also impacts on the plant footprint. The increased concentrations mean that the same total mass of solids is contained in a smaller volume, such that the footprint is smaller.
4.Better biotreatment of mbr process
the longer sludge retention times tend to provide better biotreatment overall. The conditions encourage the development of the slower-growing microorganisms, specifically nitrifiers. MBR membrane modules are especially effective at the biological removal of ammonia (nitrification).
5.Simplest Automatic operation
A STP/WWTP with MBR process can be run continuously with PLC control system. To get the most simplest operation.We have launched standard SIEMENS PLC system and SCADA System and SMS alarm etc. You can control and monitor system at anywhere and anytime only with a internet service and achieve an unattended work site.
Reviews
There are no reviews yet.