Description
Product Specification
By using Hydroblue’s state-of-the-art processing technology, The pore size of the outer and inner surface of hollow fiber membranes can be precisely controlled, the pore size control range is usually 0.01-2.0 µm. Therefore, Hydroblue produce a variety of separation membranes with suitable pore sizes according to different application scenarios.
ITEM |
Membrane Type |
|||
Ultra-low pressure UF | Pressured UF | Vacuum MBR | ||
Outer Pore size (µm) | 0.05 | 0.1 | 0.02~0.025 | 0.08-0.1 |
Inner Pore size (µm) | 0.5 | 1 | 0.2-0.3 | 5-10 |
Material | Solid PES, PSF | Solid PVDF | Crocheted PVDF | |
Nominal size (µm) | 0.05 or 0.1um | 0.02~0.025 | 0.08-0.1 | |
Fiber Diameter(mm) | 0.3~1.7mm | 0.5~1.5mm | 2.0~2.6mm | |
Porosity | 70-75% | 60% | 65-70% | |
Application | Gravity Filter Tower,
Filter Bottle, Filter Straw, filter pot, home filter etc. |
UF Membrane filter for water and waste water projects. | MBR for sewage and waste water projects |
Why We Improve
Membrane water treatment technology has the characteristics of high efficiency and energy saving. , To some certain extent, the popularization and application coverage of membrane separation technology reflects the level of energy use and environmental protection of a country and region. It is also a guarantee means for sustainable development of society. Therefore, The strategic position of membrane separation technology is very prominent.
With the application of membrane technology in water and waste water treatment, the problems of membranes, such as low strength, low flux and easy to be pollution etc have become the bottlenecks of membrane application in water treatment. And these problems are gaining more and more attention .
The key point to membrane water treatment is the structure and surface properties of the membrane material. Membrane pore size, pore distribution, pore structure and shape etc. are all important factors affecting membrane flux and membrane fouling. From the perspective of the mass transfer mechanism of the porous model, increasing the pore size will significantly increase membrane flux. For membrane filtration or MBR processes, increasing membrane flux means reducing engineering investment and floor space.
However, in actual application, it is found that membranes with large pore are much easier to occur membrane contamination such as pore occlusion and blockage than membranes with smaller pore.
The ideal membrane should have an asymmetric structure, that is, the pore size of the separation layer is far smaller than the pore size of the support layer. The micro porous structure of the support layer must have high porosity to reduce filtration resistance. At the same time, it is necessary to avoid finger-line excessively large pore structures to enhance the overall mechanical strength of the membrane.
Common membrane materials such as polyvinylidene fluoride (PVDF), polyethersulfone (PES), polysulfone (PSF), polyvinyl chloride (PVC), and polyacrylonitrile (PAN) etc. need to be carried out Hydrophilic modification to improve water flux and pollution resistance. One method is to soak the membrane hollow fiber with a hydrophilic agent , so as to be adsorbed on the surface of the membrane fiber, but the adsorbed surfactant is easily eluted during use, and permanent hydrophilicity cannot be achieved. Another common method is to add a hydrophilic polymer to the casting membrane, but it also has the problem of easy elution and lead a poor hydrophilicity of polymers.
Aiming at the shortcomings of existing technology, hydroblue’s ultra-hydrophilic hollow fiber membrane with gradient pore structure not only has the properties of ultra-high strength, super hydrophilicity, ultra-low pressure drive or zero pressure drive and ultra-high water flux, but also has particularly good anti-pollution properties.
What We Are Doing
During the hollow fiber spinning process, the amphiphilic modified silicone polymer tends to migrate to the water phase, thereby forming a gradient distribution in the radial direction of the membrane casting liquid. This technology makes use of this characteristic of amphiphilic modified silicone polymer, by adjusting the length of the hydrophilic segment and the hydrophobic segment and the ratio of the number of relative repeating segments, so as to precisely control its gradient distribution in the radial section of the casting membrane liquid. to realize the difference of water increment velocity at different parts of the radial section of the casting membrane liquid, and a super hydrophilic hollow fiber membrane with a gradient pore structure is prepared. Furthermore, because the hydrophobic group of the amphiphilic modified silicone polymer can form a strong hydrophobic interaction with the polymer membrane bulk material, the amphiphilic modified silicone is tightly combined with the polymer membrane material without being lost. So the attenuation of the hydrophilicity of the polymer film is avoided.
The ultra-hydrophilic gradient pore hollow fiber membrane contains amphiphilic modified silicone material. The gradient pore is a micro-nano bead network structure with a pore diameter increasing along the radial section of the hollow fiber membrane from the outer surface layer to the inner surface layer.
The structure refers to a three-dimensional network structure composed of microspheres with approximately spherical smooth membrane holes interwoven. This structure avoids pore cracks, uneven thickness and other surface defects which normally found in the microstructure of traditional membrane materials, so it has more superior mechanical properties; the micronano beads network structure (Figure1) is gradually increase from the outer surface to the inner surface along the radial section of the hollow fiber membrane. this network structure can significantly reduce the water permeation resistance, thereby significantly increasing water flux.
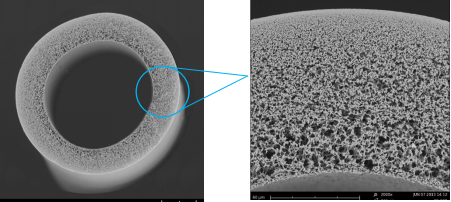
In this technology, the amphiphilic modified silicone material provides excellent and continuous hydrophilicity for the hollow fiber membrane, thereby reducing the water permeability resistance and improving the membrane’s anti-fouling ability.
In this technology, the amphiphilic modified silicone material provides excellent and continuous hydrophilicity for the hollow fiber membrane, thereby reducing the water permeability resistance and improving the membrane’s anti-fouling ability.
Reviews
There are no reviews yet.